In the expansive field of material processing, the lab roller ball mill stands as a cornerstone technology, employed across various industries and research disciplines. This versatile equipment, designed for particle size reduction, mixing, and blending, plays a crucial role in shaping the properties of countless products. This article will delve into the world of lab roller ball mills, exploring their working mechanisms, their diverse applications, and the critical factors that influence their selection and operation. We aim to provide a comprehensive guide to understand why lab roller ball mills are so essential in modern manufacturing and scientific endeavors.
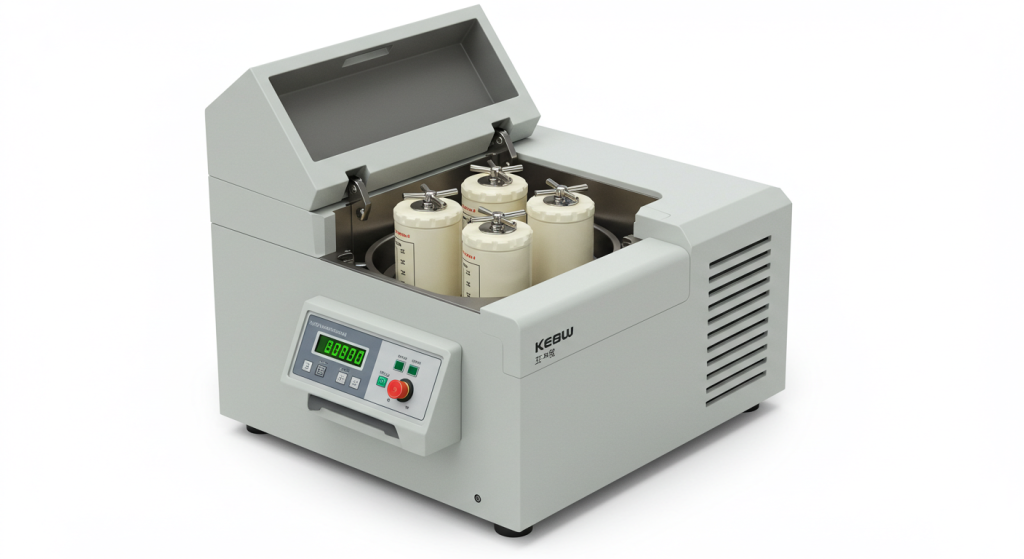
Understanding the Basic Principles of a lab roller ball mill
At its core, a lab roller ball mill is a type of grinder that uses grinding media (typically spherical balls made of steel, ceramic, or other durable materials) within a rotating cylinder to reduce the size of materials. The material to be ground is placed inside the cylinder along with the grinding media. As the cylinder rotates, the media tumbles and impacts the material, causing it to break down into smaller particles.
The effectiveness of a lab roller ball mill depends on numerous factors, such as the type of mill, the size and material of the grinding media, the rotation speed, and the duration of the milling process. The correct setup will allow you to achieve a wide range of particle sizes.
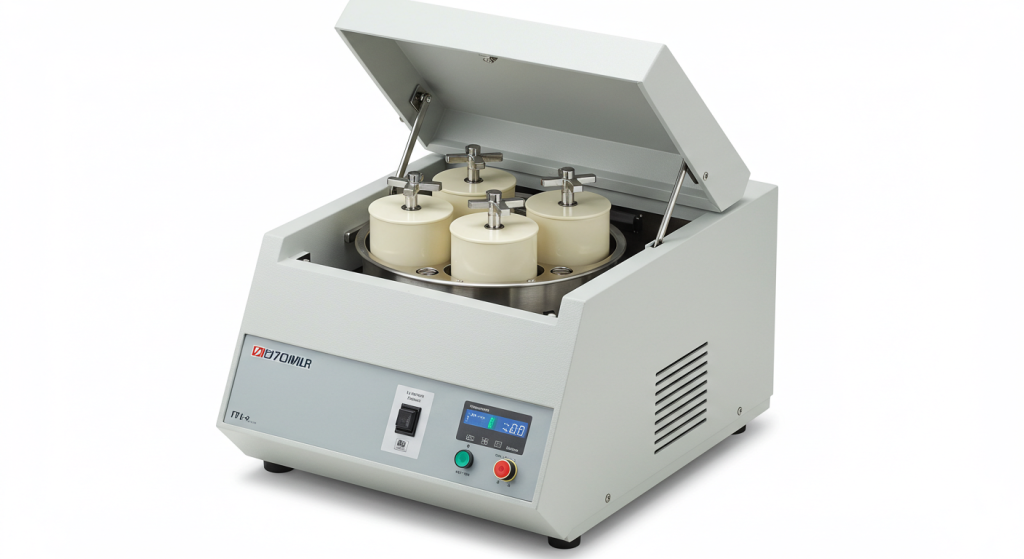
Types of lab roller ball mills: A Brief Overview
There are various types of lab roller ball mills, each suited for different applications:
Common Types of lab roller ball mills:
- Conventional lab roller ball mills: Cylindrical mills that rotate on a horizontal axis, using gravity to tumble the media.
- Planetary lab roller ball mills: Utilize a dual-rotation system, with jars on a rotating disc, resulting in high-energy impacts.
- Vibratory lab roller ball mills: Use vibrations to agitate the grinding media, often used for smaller samples.
- Attritor Mills: Use an impeller to agitate the media, suitable for a variety of grinding applications.
Key Components of a lab roller ball mill System
Understanding the fundamental components of a lab roller ball mill is key to effective operation and maintenance. These components include:
Essential Components of a lab roller ball mill:
- Mill Cylinder or Drum: The rotating container where the material and media are placed.
- Grinding Media: Usually spherical balls that provide the grinding force.
- Drive Mechanism: Motors, gears, or other systems that rotate the mill.
- Support Frame: Provides structural stability for the entire mill system.
- Discharge Mechanism: Systems for removing the milled material.
- Control Panel: Allows for monitoring and controlling the mill’s operational parameters.
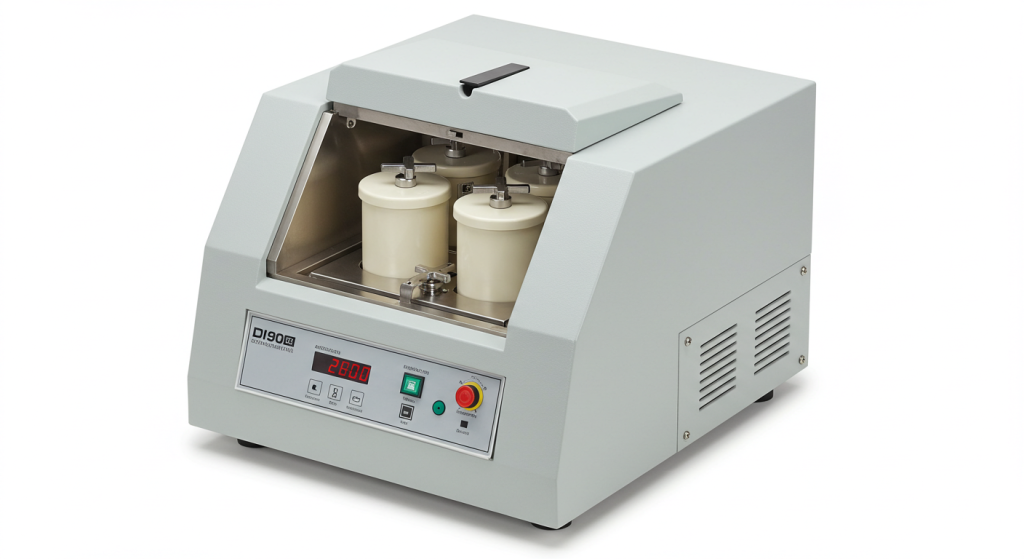
How lab roller ball mills Achieve Size Reduction
lab roller ball mills achieve size reduction through a combination of impact and attrition. As the grinding media tumbles within the rotating mill, it collides with the material and impacts it, breaking down larger particles into smaller ones. The continuous rubbing of the media also results in attrition, which further contributes to size reduction.
The balance between impact and attrition depends on factors such as the mill type, the media size and density, and the rotational speed. By carefully adjusting these parameters, different results are possible.
lab roller ball mills in Laboratory Settings
lab roller ball mills are widely used in laboratory settings for a variety of research and sample preparation applications. Their versatility and ability to process a wide array of materials makes them an important tool for many research areas.
Common Laboratory Applications of lab roller ball mills:
- Sample Preparation: Grinding samples for analysis, characterization, or further processing.
- Mixing and Blending: Creating homogeneous mixtures of powders, liquids, and pastes.
- Materials Synthesis: Creating nanomaterials, mechanical alloys, and compounds.
- Mechanical Activation: Modifying material properties through mechanical means.
- Grinding of Various Materials: Processing ceramics, pharmaceuticals, minerals, and other materials.
Industrial Applications of lab roller ball mills
On an industrial scale, lab roller ball mills are used for high-throughput grinding and processing. These applications make use of the robust nature of lab roller ball mills, and their ability to process large quantities of materials.
Common Industrial Applications of lab roller ball mills:
- Mining and Metallurgy: Grinding ores, minerals, and other materials for extraction and refining.
- Cement Production: Grinding clinker, limestone, and other materials for cement production.
- Ceramics Manufacturing: Processing raw materials for ceramic production.
- Pigment Production: Grinding and mixing pigments for paints and coatings.
- Chemical Production: Grinding and mixing chemical raw materials for various products.
- Agriculture: Grinding of grains, seeds and fertilizers for agricultural production.
The Importance of Grinding Media
The grinding media used in a lab roller ball mill has a significant impact on the efficiency and effectiveness of the milling process. Media can be made from a variety of materials including steel, ceramic, or other durable materials. Choosing the right media is critical for optimizing the milling process.
Key Properties of Grinding Media:
- Material: Different media materials (such as steel, ceramic, or zirconia) offer varying hardness and wear properties.
- Size: The size of the media impacts the grinding efficiency and the final particle size.
- Density: Higher-density media provides more forceful impacts.
- Shape: Spherical shapes are most common, but other shapes may be used for specific applications.
- Cost: The cost of the media has a direct impact on overall operational costs.
- Wear Resistance: Media must be able to resist deformation, wear and contamination of materials.
The choice of grinding media must be carefully considered, and based on the material to be milled, and the desired results.
Planetary lab roller ball mills: High-Energy Grinding
The planetary lab roller ball mill is a high-energy type of lab roller ball mill known for its powerful grinding action. It uses a unique dual-rotation system to achieve higher energy and faster milling times. The milling jars are placed on a rotating support disc, which itself is also rotating, providing a very high-energy action.
This powerful action makes the planetary lab roller ball mill well-suited for applications requiring ultrafine particle size reduction, mechanochemical reactions, and the creation of nanomaterials.
Advantages of Planetary lab roller ball mills
The planetary lab roller ball mill provides several benefits compared to conventional lab roller ball mills, due to their higher energy output.
Key Advantages of Planetary lab roller ball mills:
- Faster Milling Times: High-energy impacts lead to faster particle size reduction.
- Ultrafine Grinding: Capable of producing submicron and nanoscale materials.
- Mechanochemical Reactions: Facilitates chemical reactions through mechanical activation.
- Enhanced Efficiency: Achieves more efficient grinding and mixing.
- Precise Control: Allows for precise control of milling parameters.
Industrial lab roller ball mill Manufacturers: Key Considerations
When selecting an industrial lab roller ball mill, partnering with a reputable manufacturer is essential. Key considerations when selecting manufacturers include:
Factors to Consider when Choosing a Manufacturer:
- Experience and Expertise: Choose a manufacturer with a proven track record and substantial expertise.
- Product Quality and Reliability: Ensure that the mills are built to high-quality standards with reliable performance.
- Customization Options: Select a manufacturer that offers flexible options to meet specific requirements.
- Technical Support: Check for technical support and assistance with installation, operation, and maintenance.
- Service and Spare Parts: Look for manufacturers that provide access to spare parts and servicing.
- Cost: Consider the total cost of ownership, including initial cost and ongoing maintenance.
Maintenance and Upkeep of lab roller ball mills
Regular maintenance of lab roller ball mill equipment is critical for ensuring its long-term performance and preventing breakdowns. Proper maintenance practices will also ensure continued safety and reliability.
Key Maintenance Tasks for lab roller ball mills:
- Regular Cleaning: Always clean the mill to prevent contamination, after each use.
- Media Inspection: Regularly inspect the grinding media for wear and replace them when necessary.
- Lubrication: Proper lubrication of moving parts to reduce friction and wear is essential.
- Component Checks: Routinely check the mill for loose bolts, cracks, or other damage.
- Calibration: Check the calibration of speed controls and other parameters.
- Seal Inspection: Ensure seals are in good condition and are working properly.
Operational Considerations for lab roller ball mills
Operating a lab roller ball mill effectively involves a number of operational factors that must be carefully considered. These factors will directly impact the operation and performance of the equipment.
Key Operational Considerations:
- Loading Volume: Ensure correct loading of material and media in the milling drum or jars.
- Speed Control: Optimize the rotational speed for different materials.
- Milling Time: Adjust milling time to achieve the desired particle size and results.
- Temperature Monitoring: Monitor and control temperature for temperature-sensitive materials.
- Safety Protocols: Always adhere to safety procedures and guidelines.
Laboratory lab roller ball mills: Precision and Versatility
Laboratory lab roller ball mills are designed for a high level of precision and versatility, making them ideal for various research and development needs.
Key Features of Laboratory lab roller ball mills:
- Precise Control: Ability to set and control milling parameters for repeatable experiments.
- Small Batch Processing: Suitable for processing small sample volumes.
- Versatile Applications: Able to process a wide array of materials.
- Ease of Operation: Simple to set up and use in a laboratory setting.
- Compact Design: Designed to fit into a laboratory space with ease.
Cost Considerations for lab roller ball mill Equipment
The cost of lab roller ball mill equipment can vary significantly based on various factors, such as the type of mill, its capacity, features, and the brand. Consider not only the initial cost, but also the cost of operations.
When making your decision, you must assess both the upfront and long-term cost and benefits of the equipment to choose the right system for your needs. A careful cost-benefit analysis is critical in making the correct decision.
Conclusion
The lab roller ball mill, in its various forms, remains an indispensable tool for materials processing. From large-scale industrial applications to specialized laboratory settings, these mills provide efficient and reliable methods for particle size reduction, mixing, and blending. The planetary lab roller ball mill, with its enhanced capabilities, offers a high-energy option for more demanding applications.
Whether you choose to use a conventional lab roller ball mill or a more specialized system, a proper understanding of their mechanisms, applications, and the associated parameters is essential for achieving optimal results. The correct setup of the equipment, and following all proper procedures will help to ensure that it performs as required.
By choosing the right type of lab roller ball mill, selecting the proper media, and implementing a proper maintenance plan, users can fully utilize these versatile tools and obtain the performance required for their specific purposes. Through ongoing innovation and technology, lab roller ball mills will remain a key part of material processing for years to come.