Which is the best laboratory roller mill? When it comes to selecting the optimal equipment for precise material processing, the question of “which is the best laboratory roller mill” is paramount for researchers and developers. This article aims to provide a comprehensive guide to understanding laboratory roller mills, highlighting their advantages, applications, and the crucial factors to consider when choosing one. In addition, questions such as “Why to buy nylon roll ball mill jar” also weigh into the selection process, given its unique properties in specific lab milling operations. We will explore the nuances of roller mill technology and its alternatives, helping you make an informed decision tailored to your needs.
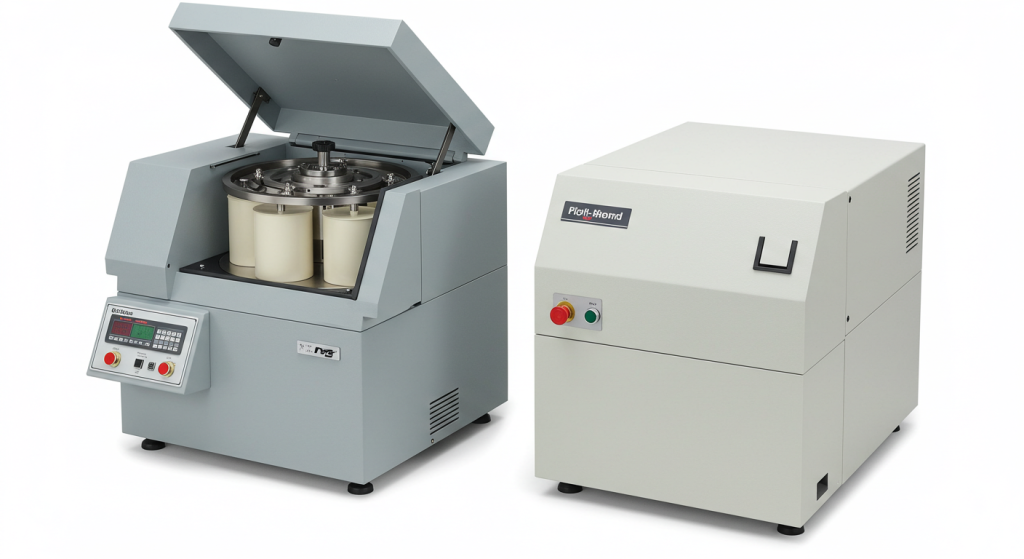
Understanding Laboratory Roller Mills: An Introduction
Laboratory roller mills are essential pieces of equipment used across diverse scientific and industrial fields. They function primarily to reduce particle size, mix substances, and achieve uniform consistency of materials. The core principle of operation involves rotating cylindrical jars on powered rollers, which agitate and grind the contents inside. This process allows for precise control over milling parameters, making it suitable for a wide range of materials from powders and granules to liquid suspensions. Roller mills are particularly valued for their ability to handle small batch sizes efficiently and provide consistent results, making them indispensable for laboratory-scale research and development.
Where to Buy Roll Ball Mill: Key Considerations
The search for “Where to Buy Roll Ball Mill” often leads to numerous suppliers, each offering models with varied specifications. However, before making a purchase, it is important to consider several key factors:
- Jar Capacity and Size: The size and capacity of the jars determine the batch size you can handle. Choose a mill that is compatible with the volume of your experiments or production runs.
- Roller Speed Control: Variable speed control allows you to tailor the milling process to different materials and particle size requirements. This ensures flexibility and optimizes milling performance.
- Material Compatibility: Consider the types of materials you will be processing and ensure the mill’s components are made from materials that can withstand chemical or physical stress, including the jar material and the roller materials.
- Ease of Use and Maintenance: Select a mill that is user-friendly, with intuitive controls and easy maintenance to keep operational downtime low.
- Safety Features: Essential safety features should be considered, such as safety guards, emergency stops, and spill containment, to protect both the operator and the mill.
- Supplier Reputation and Support: Choose suppliers with good reputation who offer technical support, warranties, and replacement parts.
An informed decision requires considering all of these aspects before selecting a roller mill that fits your needs.
Roller Mill vs. Alternatives: A Comparative Analysis
When evaluating material processing solutions, it’s crucial to compare roller mills with other available methods. This section will examine the differences between roller mills and various other types of mills.
Which is better, roller mill or hammer mill?
The question of “Which is better, roller mill or hammer mill?” depends entirely on the application. Hammer mills use impact force generated by swinging hammers to crush material, making them ideal for coarse grinding of dry and friable substances. Roller mills, on the other hand, apply compressive forces to grind materials between rotating rollers or jars, making them more suitable for fine grinding and mixing of various materials. Hammer mills are commonly used for size reduction of wood, grains, and other coarse materials, while roller mills are preferred for processes that require fine and uniform particle sizes, such as powder mixing and dispersion.
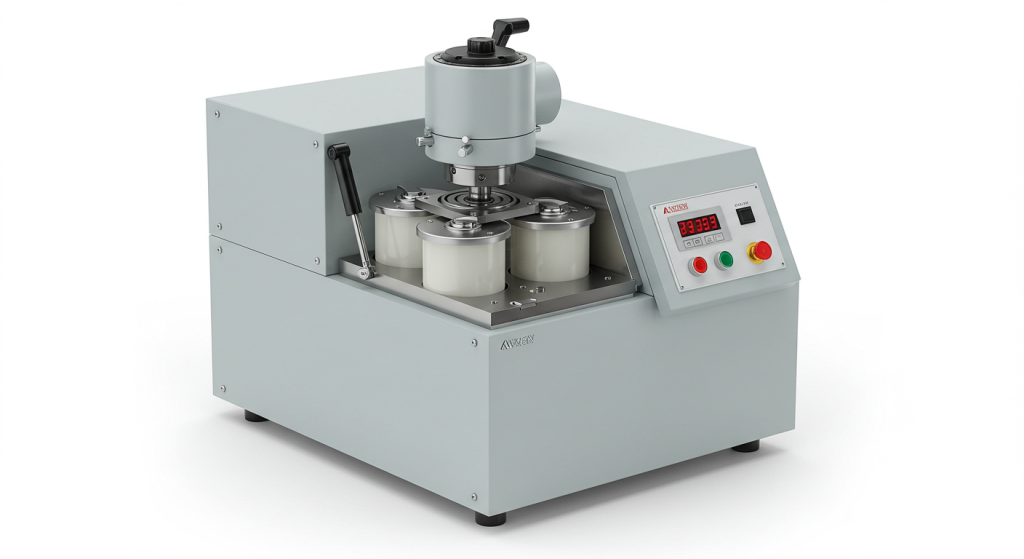
What is the difference between a roller mill and a stone mill?
Another important comparison is between “What is the difference between a roller mill and a stone mill?”. Stone mills employ two large stones (one stationary and one rotating) to grind materials, traditionally used for milling grains and producing flour. They are known for producing a less heated and finer final product, which can be better suited for nutritional and flavor retention. Roller mills, using metal or ceramic rollers, can provide greater control and uniformity in particle size and are more suited for larger volumes and various materials. Stone mills are mostly used for food applications, while roller mills are more common in various laboratory and industrial processes. The choice between stone and roller mills depends on the specific product requirements and the scale of operation.
What is the difference between ball mill and roller mill?
A key question often asked is “What is the difference between ball mill and roller mill?”. As discussed in earlier sections, both mills achieve size reduction via mechanical action. The primary differences relate to the mechanism of grinding and the scale of operation. Ball mills typically employ a rotating drum filled with grinding media (balls) that crush and grind materials through tumbling action. They are used for both large and small-scale applications. Roller mills, however, utilize rotating rollers to rotate jars filled with materials and grinding media, making them more appropriate for smaller batches and lab environments, with more precise control over the milling process. Ball mills can handle larger capacities and can be more suitable for harder and abrasive materials, while roller mills are preferred for precise mixing and grinding of various material types in a controlled setting.
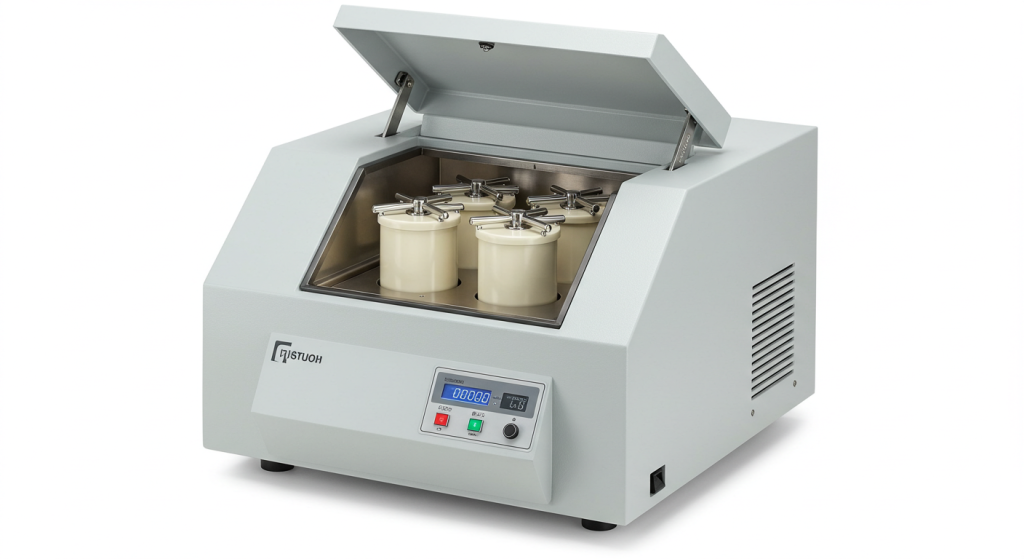
Advantages of Laboratory Roller Mills
Laboratory roller mills offer a range of advantages that make them ideal for many applications. The precision and control they offer are vital in research and development settings. Here are some key advantages:
- Precision Control: The ability to control roller speed and jar rotation allows for fine-tuning of the milling process, achieving the desired particle size and consistency.
- Uniform Mixing: Roller mills achieve uniform dispersion and mixing of materials, crucial for various applications in pharmaceuticals and chemical industries.
- Small Batch Processing: Ideal for lab research and small-scale production that require only small amounts of material for testing or development.
- Versatility: Roller mills can handle a broad array of materials, including powders, granules, and liquid suspensions, accommodating various research and production needs.
- Ease of Operation: They are user-friendly, with simple controls and minimal maintenance requirements.
- Consistent Results: Roller mills provide consistent and reproducible results, which is essential for scientific research and quality control.
The Anatomy of a Lab Roller Mill
A lab roller mill is composed of several key components that work together to achieve the desired milling outcome. Understanding these parts is crucial for operating and maintaining the mill.
Exploring Disadvantages of Roller Mills
What are the disadvantages of roller mills?
While roller mills are versatile and effective, they are not without drawbacks. A thorough understanding of their limitations helps in making informed choices:
- Lower Throughput: Compared to larger industrial mills, roller mills have a relatively lower processing throughput.
- Limited for Very Hard Materials: While suitable for a wide range of materials, roller mills may not be as effective for extremely hard or abrasive materials as compared to hammer or ball mills.
- Potential for Material Buildup: Material accumulation on the rollers or within the jars can affect milling efficiency and require regular cleaning.
- Noise Levels: Operation of roller mills can sometimes generate considerable noise, which may need to be mitigated in certain lab environments.
- Jar and Roller Wear: Frequent use can cause wear and tear of the jars and rollers, requiring periodic replacement and maintenance.
Addressing the Limitations
By selecting the right materials for milling jars and rollers, as well as optimizing process parameters, some of the drawbacks of using a roller mill can be addressed. Regularly checking and maintaining the machine is critical for continuous and optimized performance. In situations that demand very hard materials to be processed, considering alternative milling options may be better.
Specific Applications of Lab Roller Mills
Laboratory roller mills are versatile and find applications across numerous fields. Here are some key uses:
- Pharmaceuticals:
- Grinding and mixing of active pharmaceutical ingredients (APIs)
- Formulating suspensions, emulsions, and ointments
- Preparing samples for drug analysis and development
- Cosmetics:
- Producing fine and uniform pigments for makeup
- Mixing raw materials for creams, lotions, and other cosmetic products
- Creating finely dispersed substances for better texture and application
- Chemicals:
- Mixing and grinding raw materials for chemical synthesis
- Preparing samples for chemical analysis
- Formulating paints, coatings, and inks
- Material Science:
- Processing ceramics, polymers, and composites
- Preparing materials for research and analysis
- Creating uniform blends of different materials
- Research and Development:
- Conducting material testing and analysis
- Experimenting with various milling parameters to optimize particle size and consistency
- Developing new materials and processing methods
Milling Jars: Understanding Material Choices
The Crucial Role of the Milling Jar
The material of the milling jar is crucial in roller mill applications. It directly influences the milling process and the end product. Some common materials include:
- Glass: Suitable for non-reactive and non-abrasive materials, it provides a visible milling process but may break with high-impact forces.
- Ceramics: Such as alumina and zirconia are favored for high hardness, chemical inertness, and wear resistance, making them ideal for precision milling and avoiding contamination.
- Stainless Steel: Highly durable and versatile, it is suitable for most milling operations. However, it may not be appropriate for highly sensitive applications where contamination is a concern.
- Polymers (Nylon and PU): These offer flexibility, chemical resistance, and reduced contamination and are suitable for various milling processes. The specific choice depends on the material being milled and the desired end-product purity.
Why to buy nylon roll ball mill jar
The question “Why to buy nylon roll ball mill jar” arises often because nylon is a widely used polymer in lab equipment. Nylon offers several benefits such as good chemical resistance, low weight, and decent durability. Its smooth surface helps to prevent material build-up and reduces contamination, making it a valuable option for many laboratory settings. While nylon jars are a common choice, other materials like PU may offer superior properties for specific milling applications. Understanding the nuances of each material is key to making the right purchase decision.
Optimizing Roller Mill Performance
To achieve optimum milling results, some key strategies can be employed:
- Choosing the Correct Grinding Media: Selecting the right type of grinding media (balls) is critical. The material, size, and shape of the grinding media affect the particle size and the speed of the milling process.
- Optimizing Jar Filling Level: The correct amount of material and media in the jar is crucial. Over or underfilling can impact grinding efficiency.
- Adjusting Roller Speed: The speed of the rollers should be adjusted according to the properties of the material and the desired particle size.
- Maintaining the Mill: Regular maintenance, such as cleaning the mill and its components, and lubricating moving parts, ensures optimal performance and longevity.
- Monitoring the Milling Process: Observing the milling process ensures that the desired results are being achieved and any issues can be addressed promptly.
By following these guidelines, users can maximize the capabilities of their laboratory roller mills.
Future Trends in Laboratory Roller Mills
Technology is always evolving, and laboratory roller mills are no exception. Current trends include:
- Smart Controls and Automation: Incorporating sophisticated control systems with automation capabilities to allow for more precise control over milling processes.
- Advanced Materials: Exploring new materials for rollers and jars that provide enhanced performance, durability, and reduced contamination.
- Compact Designs: Smaller, more portable roller mills that are easy to transport and place in laboratory environments.
- Energy Efficiency: Designing more energy-efficient mills to reduce operating costs and environmental impact.
- Improved Safety Features: Adding enhanced safety mechanisms to protect the operators better and reduce any risks.
These advancements are designed to make roller mills more efficient, easier to use, and better suited for a wider range of applications.
Conclusion
In conclusion, understanding “Which is the best laboratory roller mill” requires evaluating your specific needs and the characteristics of your milling material. A well-chosen roller mill can provide consistent, reliable, and precise results in various applications. Whether you need a basic unit for simple mixing or an advanced model with precise control and enhanced features, selecting the right roller mill involves several key considerations, including jar capacity, speed control, material compatibility, and maintenance. Furthermore, while materials like nylon offer benefits in specific cases, the broader context of performance, material compatibility, and safety, must be considered when evaluating “Why to buy nylon roll ball mill jar”. Finally, remember that when searching “Where to Buy Roll Ball Mill”, carefully consider all factors before making a final purchase. Our aim is to guide you in making the most informed choice for your particular needs. By keeping in mind the key points discussed, you are well-equipped to select the ideal roller mill for your needs. The optimal mill ensures efficient and high-quality material processing for your laboratory work.
Feature | Roller Mill | Hammer Mill | Stone Mill |
---|---|---|---|
Grinding Action | Compressive Force via Rollers | Impact Force via Hammers | Grinding between Stones |
Best Suited For | Fine Grinding, Mixing | Coarse Grinding | Food Grains |
Material Type | Various, incl. powders, granules, liquids | Dry, Friable Materials | Grains |
Particle Size | Fine, Uniform | Coarse | Finer for grains |
Primary Use | Lab and Small Batch Production | Industrial Applications | Food Processing |
Throughput | Lower | Higher | Moderate |