Why to buy our PU roll ball mill pot? When considering a reliable and efficient solution for your milling needs, our Polyurethane (PU) roll ball mill pot stands out as a superior choice. Its robust construction, excellent chemical resistance, and smooth interior make it ideal for a wide range of applications, ensuring consistent and high-quality results. Moreover, the question of “Why to buy nylon roll ball mill jar” is also a valid one, and while nylon has its benefits, the unique properties of PU often make it the preferred material in many demanding milling environments. This article will explore the advantages of our PU roll ball mill pot, compare it to other milling options, and delve into the finer details of ball milling technology.
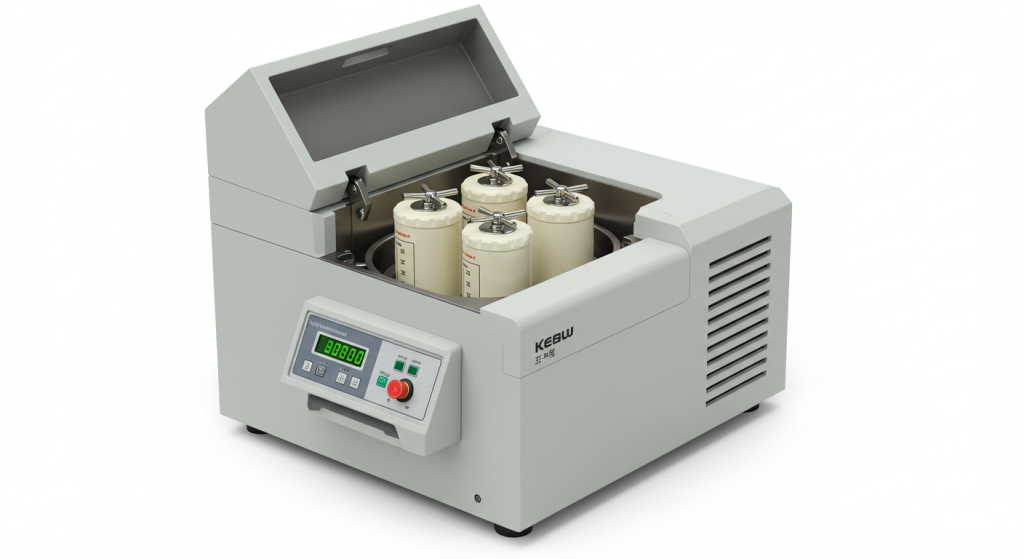
Understanding Ball Milling: A Comprehensive Overview
Ball milling is a versatile size reduction method extensively used across various industries. It employs the principle of impact and attrition, where grinding media (balls) inside a rotating jar or drum crush and grind the material placed within. The result is a fine powder or slurry depending on the process parameters. There are two main types of ball mills: planetary ball mills and roller ball mills (also known as jar mills). While both achieve similar results, their operation and applications differ significantly.
What is the difference between ball mill and roller mill?
The fundamental difference between a ball mill and a roller mill lies in their mode of operation and the scale of production they typically handle. A traditional ball mill is a large, rotating drum filled with grinding media. The drum itself rotates, causing the media to tumble and grind the material inside. Roller mills, on the other hand, employ smaller jars (like our PU roll ball mill pot) that are placed on rotating rollers. The rollers cause the jars to rotate, thus grinding the contents. In short, the primary difference is the scale and mechanism of rotation—one rotates a drum while the other rotates jars. Roller mills are generally used for smaller batch sizes and laboratory settings, whereas ball mills are often employed for larger-scale industrial production.
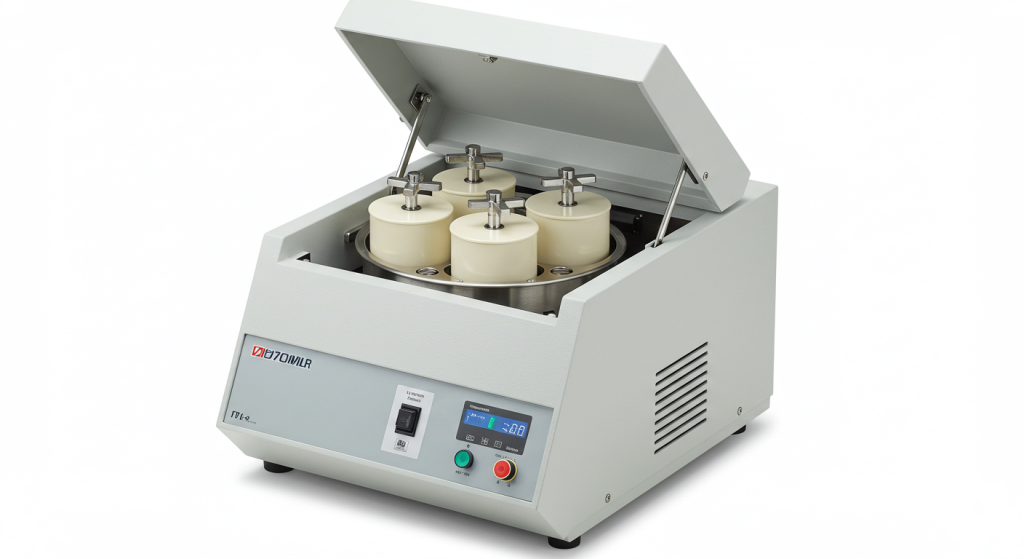
What are the advantages of the ball mill?
Ball mills offer several advantages that make them essential in many industries:
- Versatility: They can grind a wide variety of materials, from brittle substances to tougher ones.
- Fine Grinding: They can achieve very fine particle sizes, often in the nanometer range, which is crucial for many applications.
- Scalability: They come in a range of sizes, from small laboratory mills to large industrial units.
- Batch and Continuous Operations: Ball mills can be used for both batch processing and continuous grinding operations.
- Controlled Environment: They allow for controlled atmospheres, which is important for processing materials that are sensitive to oxidation or contamination.
Exploring Roller Ball Mills: Detailed Analysis
Roller ball mills, often the choice for lab-scale research and small-batch production, offer a different set of advantages. The use of a PU roll ball mill pot is one example of how specialized containers can improve results. The compact size and ease of use of roller mills make them highly desirable for R&D purposes. Here is a more detailed analysis:
Roller Ball Mill Operation
A roller ball mill consists of a rotating frame with rollers that support cylindrical jars, like our featured PU roll ball mill pot. When the rollers turn, they rotate the jars, causing the media and material inside to be crushed. The grinding action is similar to that of a large ball mill, but the scale is reduced, and the process is more manageable for smaller batches. Many laboratories ask “Where to Buy Roll Ball Mill,” and the answer is that numerous suppliers specialize in providing this essential lab equipment. They offer a variety of models, catering to different jar sizes and processing needs. When selecting a roller ball mill, the material of the milling jar, like our high-quality PU options, is a crucial consideration.
Advantages of Roller Ball Mills
- Compact Size: Ideal for laboratory and small production settings.
- Ease of Use: Simple operation and maintenance make them user-friendly.
- Batch Processing: Perfect for handling smaller batch sizes.
- Flexibility: Can accommodate a range of jar materials and sizes.
- Cost-Effective: Lower upfront investment compared to larger ball mills.
The Role of the Milling Jar
The milling jar is a critical component of the roller ball mill. The material of the jar affects the milling process and product quality. Common jar materials include stainless steel, ceramic, and polymers like PU and nylon. Each material offers unique properties regarding chemical resistance, hardness, and wear resistance. For example, while a nylon roll ball mill jar is suitable for certain applications, our PU roll ball mill pot offers a compelling combination of durability, resistance, and performance for many types of milling.
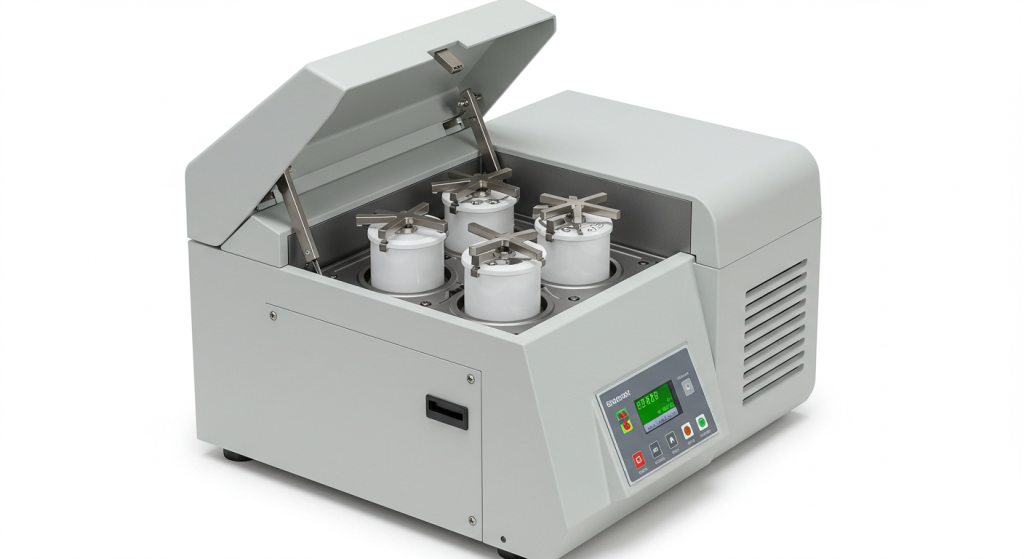
Delving into Grinding Media: What Are the Best Balls for a Ball Mill?
Understanding Ball Mill Media
The grinding media, typically balls, play a key role in the ball milling process. The material, size, and shape of the grinding media influence the efficiency of milling. Common media materials include:
- Steel: Suitable for most applications, durable, and cost-effective.
- Ceramic (Alumina, Zirconia): Offers good chemical resistance, low contamination, and high hardness.
- Tungsten Carbide: Extremely hard, suitable for grinding very hard materials.
- Glass: Low hardness, used for softer materials or for applications where metal contamination is not desirable.
What are the best balls for a ball mill?
The best type of grinding media depends on the material being processed and the desired end product. For example, for applications requiring high purity and minimal contamination, ceramic media like Zirconia Ball Mill jars and media are the preferred choice. Zirconia’s high hardness and inert nature make it suitable for high-quality, fine-milling needs. On the other hand, for applications where abrasion is not a concern, steel media can be a more cost-effective solution. The size of the media is also critical. Smaller balls provide finer grinding, while larger balls deliver higher impact energy for coarser materials. The choice of media must be carefully considered to achieve optimal milling results. The selection of the appropriate grinding media is critical for efficient and high-quality milling.
Considering the Drawbacks: What are the disadvantages of a ball mill?
Ball Mill Disadvantages
While ball mills are highly useful, they also have some limitations that should be considered:
- Slow Grinding: Ball milling can be a slow process compared to some other methods.
- Energy Consumption: They can consume a significant amount of energy.
- Noise Pollution: Ball milling can be a noisy operation.
- Media Wear: The grinding media can wear down, leading to contamination in the milled product.
- Temperature Increase: Milling can generate heat, potentially affecting heat-sensitive materials.
Addressing the Challenges
Careful process optimization can mitigate many of these disadvantages. For example, by selecting the correct milling media and jar material, the contamination issue can be minimized. Utilizing cooling systems or taking breaks during milling helps reduce temperature increases. When assessing the question “Why to buy nylon roll ball mill jar,” it’s important to consider how well it addresses temperature and wear issues compared to other materials like PU.
Deep Dive into Specific Ball Milling Technologies
Planetary Ball Mill
Planetary ball mills operate differently from traditional ball mills and roller ball mills. In a planetary ball mill, the jar rotates on its own axis while simultaneously orbiting around a central axis. This dual rotation mechanism generates significantly more energy than a simple rotating drum or jar, allowing for much faster and finer grinding. Often, questions arise regarding “Where to Buy Roll Ball Mill,” but it’s important to understand that planetary mills serve a different purpose than roller mills, with both being vital to laboratory and small-scale production. Planetary ball mills are typically used for very fine grinding of hard materials in R&D and quality control labs. When it comes to high-energy milling, the planetary setup is often the preferred option.
Rotary Ball Mill
A rotary ball mill is another type of traditional ball mill where the drum rotates around a horizontal axis. This simple design is reliable and efficient for a wide range of grinding applications, making it a popular choice for various industries. These machines can handle large quantities of material, making them suitable for industrial-scale operations. Whether it’s a lab-scale unit or an industrial model, the basic principle of a rotating drum filled with grinding media remains the same. They are used in cement production, mining, and numerous other sectors. For many applications, the use of specialized mill jars like our PU roll ball mill pot can further enhance process efficiency and maintain product purity.
MSE Planetary Ball Mill
The MSE Planetary Ball Mill, similar to other planetary models, uses the dual rotation mechanism to deliver efficient and high-energy grinding. MSE, like other brands, offers various models and sizes, catering to a range of research and industrial needs. Such mills are characterized by their precision control and superior performance when it comes to ultra-fine grinding applications. If you are seeking an MSE planetary ball mill, similar models are available to address various applications. One key advantage of planetary ball mills is the control they offer over particle size and energy input. Understanding the differences between planetary and traditional ball mills is crucial when choosing the right equipment for a specific application.
Materials and Applications: The Role of the Milling Jar
Ceramic Ball mill media
Ceramic ball mill media, including materials like alumina and zirconia, are favored for applications requiring high purity and minimal contamination. These materials are inert, hard, and resistant to wear, making them ideal for grinding sensitive or valuable materials. The media’s properties also contribute to finer milling results, which is crucial for many applications in pharmaceuticals, cosmetics, and advanced materials processing. The choice of media depends greatly on the end application of the milled product. The decision of using ceramic grinding media alongside materials like our PU roll ball mill pot is often a balance between desired results and overall budget. The benefits of ceramic media often justify the investment in high-precision applications. The inertness of ceramic media also makes it ideal for situations where chemical contamination must be avoided.
Ball mill powder
The final product of ball milling is often a fine powder. Ball mill powder is used in a plethora of industries. The fineness and consistency of the powder produced via ball milling make it a versatile material for various applications including pigments, pharmaceuticals, battery materials, and more. The quality of the final powder is determined by several factors, including the ball mill setup, the media used, the material being processed, and the milling time. Different applications require different particle sizes, shapes, and purities, making process optimization critical. Whether it’s for lab research or industrial-scale production, the control over particle size achieved with ball milling makes it a primary method for achieving ultra-fine powder.
Applications of Ball Mills
Ball mills find applications in a diverse range of industries, including:
- Mining: Grinding ores into fine powders for mineral extraction.
- Cement Production: Grinding clinker into cement powder.
- Ceramics: Producing raw materials for ceramic products.
- Pharmaceuticals: Milling active pharmaceutical ingredients.
- Cosmetics: Grinding raw materials for creams, lotions, and makeup.
- Paints and Coatings: Grinding pigments for paints and coatings.
- Advanced Materials: Grinding materials for electronics and energy storage.
Why to buy our PU roll ball mill pot? (Revisited)
Returning to the initial question, “Why to buy our PU roll ball mill pot?,” it is essential to highlight its unique advantages. Our PU roll ball mill pot provides:
- Excellent Chemical Resistance: PU is resistant to a wide variety of chemicals, making it suitable for various applications.
- Durability: PU is highly durable and can withstand the stresses of ball milling.
- Smooth Interior Surface: The smooth interior of the pot minimizes material buildup and makes cleaning easy.
- Low Contamination: PU provides minimal contamination compared to other materials.
- Versatility: It can be used for milling a variety of materials, from soft powders to harder granules.
- Cost-Effectiveness: PU provides a good balance between performance and cost, making it a cost-effective option for many applications.
The question of “Why to buy nylon roll ball mill jar” is also important. However, PU often offers greater chemical resistance, abrasion resistance and enhanced performance compared to nylon in various milling situations. This makes our PU roll ball mill pot a very practical and reliable choice for many labs and small-scale production facilities. Additionally, when seeking “Where to Buy Roll Ball Mill,” always remember that the choice of material is as important as the mill itself, and the choice of jar material is a key factor to the overall success of the milling process. Our PU mill jars are designed for consistent, high-quality results. We ensure that our product meets the needs of our customers by offering a superior solution for material processing. The robust and versatile nature of our PU mill jars makes them ideal for a wide variety of applications.
The use of high-quality milling jars is an investment in your grinding process, ensuring optimal efficiency, consistent results, and reduced contamination. Therefore, choosing our PU roll ball mill pot is a wise choice when looking for a dependable and adaptable solution for ball milling.
Feature | PU Roll Ball Mill Pot | Nylon Roll Ball Mill Jar |
---|---|---|
Chemical Resistance | Excellent | Good |
Durability | High | Moderate |
Smooth Interior | Yes | Yes |
Contamination | Low | Low |
Versatility | High | Moderate |
Cost-Effectiveness | High | Moderate to High |
Abrasion Resistance | High | Moderate |
When considering purchasing lab equipment and “Where to Buy Roll Ball Mill” becomes a question, remember that selecting the right equipment for your needs is critical. Considering a high-quality PU mill pot offers long-term reliability. It’s a worthwhile investment for any laboratory or small-scale production facility that needs precise and reliable milling. Whether your focus is on R&D or small batch production, the benefits of using a well-designed PU ball mill jar are clear.